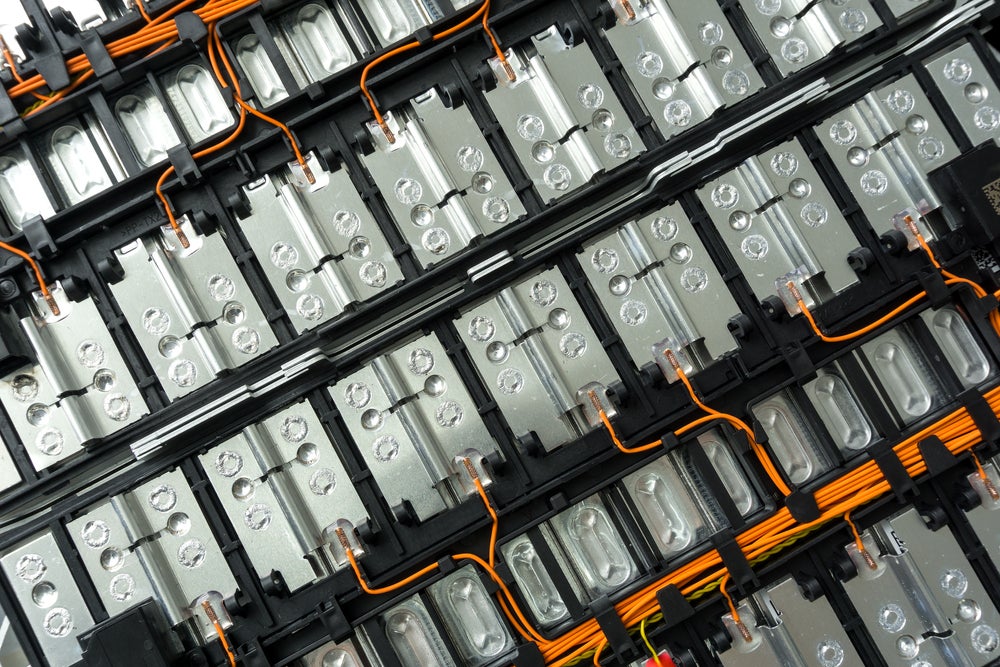
EV Battery Makers Are Grappling with Graphite
Graphite is used for the negative end of a lithium-ion battery, known as the anode. Currently, 85% of graphite comes from China. A rival to naturally occurring graphite is its synthetic equivalent, but green considerations around its production offer significant challenges for the auto sector. Al Bedwell, director, global powertrain at LMC Automotive, considers the alternatives to graphite in EV batteries
Graphite makes up the vast bulk of the anode (95%) of a typical Li-ion battery fitted to a battery electric vehicle (BEV) and approximately 1kg of graphite is needed per kWh of battery energy making it, by weight, the most significant element of the battery cell.
China has reached a position of dominance in the supply of the type of high-grade processed graphite needed for BEV batteries, with estimates suggesting that it accounts for circa 85% of global supply.
Not only does it have significant reserves of natural graphite, but it has a near-monopoly on the industrial processes required to transform the material from mined (‘flake’) state to the highly pure spherical graphite needed to form the battery anode.
There is an alternative to natural graphite, and that is synthetic graphite made using petroleum as a feedstock.
Battery cell production
Battery cell makers prefer synthetic graphite because its more uniform structure is conducive to longer battery operational life. Estimates indicate that it has overtaken natural graphite in current BEV Li-ion battery production and anodes are often made up of a mixture of natural and synthetic graphite.
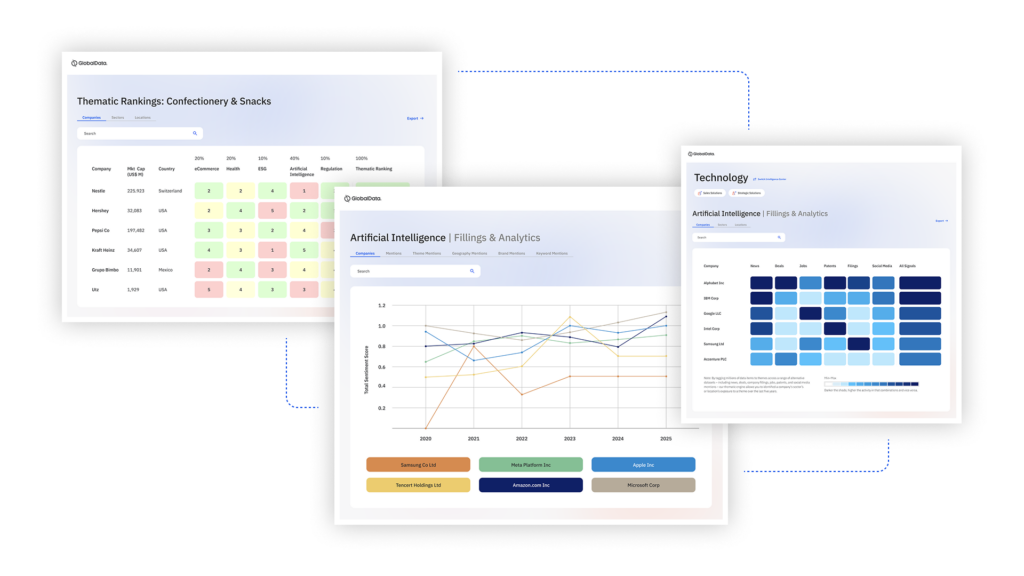
US Tariffs are shifting - will you react or anticipate?
Don’t let policy changes catch you off guard. Stay proactive with real-time data and expert analysis.
By GlobalDataHowever, it is also more expensive than natural graphite and even less environmentally friendly than natural graphite in its sourcing and production methods. And, as it happens, China also dominates the global supply of synthetic graphite. The chart shows how demand for battery-grade graphite for the BEV sector would grow this decade assuming it was to remain the sole anode material.
Only in recent times, driven by anticipated growth in graphite demand from the battery vehicle sector, are projects capable of providing battery-grade graphite at scale being set up outside of China.
Australia is a focus, but projects are being developed in Canada, Alaska, Africa and Europe. Rising graphite demand is making these projects viable but also putting up the price of battery-grade graphite, especially when it is produced in territories where by-products of refining are more tightly controlled (than they are in China).
These issues of cost, battery performance (is there a better alternative to graphite?), ESG concerns, and security of supply have led to a long search for alternatives to graphite as an anode material.
Battery performance
Perhaps the key driver is battery performance, though growing stress on the graphite industry and its dominance by China shouldn’t be ignored.
While Li-ion batteries have (until recently at least) fallen in cost, the rate at which their performance can improve using current technologies has slowed.
At the same time, the industry has geared up massively to produce Li-ion batteries rather than any other type. Much work has been carried out to alter cathode chemistries whether to improve performance (range and charging time) or to avoid using contentious materials (like cobalt). But there are limitations and trade-offs in what can be achieved. It’s a bit like buying a new house: You can have space, location or affordability but you can’t have all three at the same time.
With conventional Li-ion batteries it’s a trade-off between energy storage, durability, and pack weight/size. It’s been known for a long time that using silicon as an anode material can significantly improve energy density – many more lithium atoms can be stored in silicon than in graphite. In fact, up to 10% silicon is blended with graphite anodes today for this very purpose. The downside of pure silicon anodes though has always been the tendency of silicon to expand and contract during the charge and discharge cycle (by up to 300%) leading to premature cell failure.
The problem to be solved, therefore, was to create a silicon-based material that would offer the energy storage benefits of silicon versus graphite while remaining stable over thousands of charge/discharge cycles. This now appears to have been achieved, with companies such as US-based Sila Nanotechnologies (Sila) leading the way. Scaling up the production of such anode material has reached a point where Mercedes-Benz has specified a silicon-anode battery from Sila for its forthcoming all-electric G-Wagon.
This looks like a significant breakthrough, with the early application at the heavier end of the electric vehicle spectrum where the improved energy density helps mitigate increasingly heavy and bulky batteries.
Going back to the trade-off point earlier, what this new anode material does is significantly reduce the amount of battery weight/size that has to be gained to get a higher-capacity battery.
As for cost versus graphite, this has yet to be fully revealed but we can assume that, given the tiny scale of silicon anode production as the sector ramps up, it may initially be higher than a graphite cell. But the raw material is abundant and cheap (silicon is the second most abundant element in the earth’s crust after oxygen) so cost will largely depend on scaling the industrialisation process.
Finally, a key point to make is that substituting silicon for graphite doesn’t mean that cell makers need to drastically reconfigure their Li-ion gigafactories. Given the vast investment going into the sector, that’s a good thing.
Can the UK auto industry survive without a vast domestic battery manufacturing base?