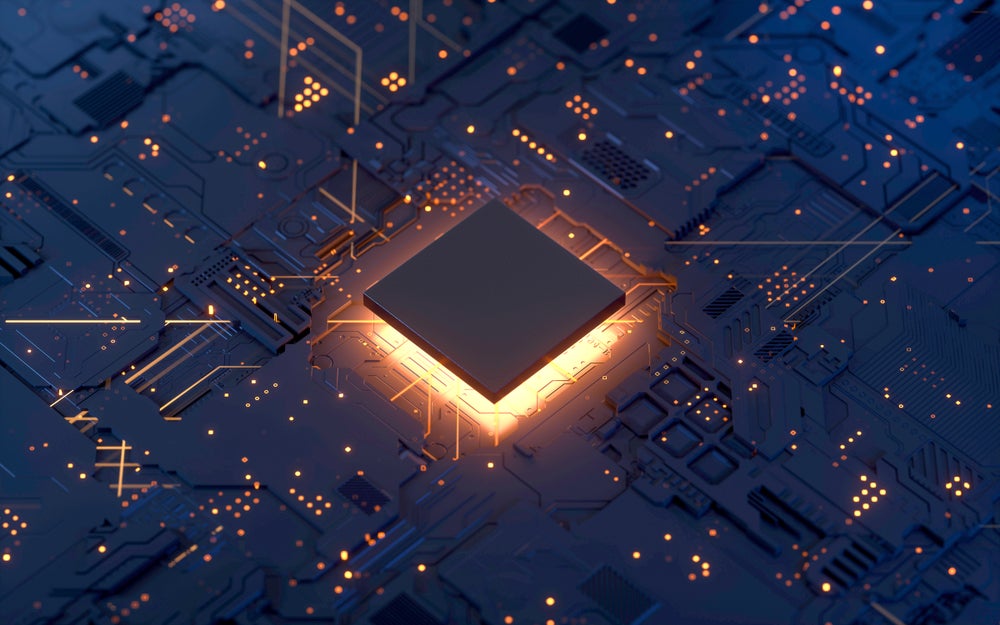
In the aftermath of the pandemic, the car industry has been hit from the left field by a sudden shortage in essential raw materials, a crisis that will have a much wider knock-on effect.
Cars haven’t always had microchips in, but the use of microchips in cars is only going to grow. Look at the key fob you use to remotely lock and unlock your car. In that alone, there are four main microchips, alongside numerous other electronic components. Therefore, as the use of chips has grown, so has the interdependency between chip manufacturers and the OEMs supplying other car parts.
This means that the entire industry, from parts manufacturers through to dealers and lenders, has been hit hard by the recent shortage of essential semiconductor materials.
“The shortage of semiconductors – the material that houses multiple circuits on ‘chips’ used in electronic devices – is currently having an impact on the supply of new vehicles to the UK, including on those looking to lease,” explains Paul Harrison, head of strategic partnerships at Leasing.com.
“The immediate impact has been the delay to lead times for the production of brand-new vehicles. Depending on the exact spec of new vehicles, factory lead times have been extended by a further six months. Manufacturers are then rationing the chips they do have access to by using fewer of them in lower-spec models and saving chips for higher-margin trims.”
While this seems like a high-tech problem, the biggest shortfall for the auto industry has been in microchips that are over 20 years old.
Geoff Cousins is an expert on the automotive industry, as chairman of the G & P Group and former managing director of Jaguar UK.
“A big challenge is how to address the type of computer chips that are in most demand and establish an accurate picture of those that will be needed in auto production in coming years,” Cousins points out. “In fact, many electric vehicles are expected to use more of the less advanced chips as well, which will imply higher demand.”
A perfect storm
The shortage on its own is a challenge, but its timing couldn’t be worse.
“The auto industry is facing a perfect storm,” Cousins tells us. “In the past year manufacturers have slashed production to match falling demand while the demand for consumer electronics has grown substantially.
“Many automotive manufacturers cancelled orders in response to production cuts and when demand in Q4 2020 picked up they tried to scale up chip supply. The chip makers however had already prioritised consumer electronic orders, which make up a far larger and more profitable segment of their business.”
Harrison recalls the stop/start effect Covid-19 had on vehicle production throughout 2020 and early 2021: “With motor manufacturers forced to cancel or delay orders for all vehicle components, and with semiconductors used in the production of a huge range of other goods, semiconductor manufacturers have accepted orders from other sectors. When motor manufacturers resumed production, they found themselves at the back of the queue and the semiconductors needed were not readily available.”
To make things worse, the auto industry tends to rely on a small handful of suppliers – Taiwan Semiconductor Manufacturing Company (TSMC) is the biggest and most are based in the Far East. The issue is affecting the auto industry around the world, with the possible exception of China where potential USA sanctions drove them to stockpile before the shortage hit.
“There is large pent-up demand which means we will go from famine to feast as soon as there is a free supply of microchips”
Cousins argues that the impact on the auto industry is going to be even bigger than first imagined. There will be global production losses of 2m vehicles in 2021, including 450,000 units in Europe, including the UK.
Audi has announced that it is laying off 10,000 people in Germany in June. JLR has narrowed its production to high-end, high-value vehicles to minimise losses and get the most value from the chips it has.
Meanwhile, businesses in the fleet industry are unable to replace vehicles, leading to increased maintenance costs. The majority of auto leaders expect this situation to continue for at least the next six months.
“Extended lead times for factory orders will have turned some consumers to the used car market for their preferred model and we’ve seen increases in used car prices,” says Harrison. “However, the shortage has not impacted all parts of the UK new car market. Many manufacturers stockpiled new units ahead of Brexit and vehicle reserves have lasted longer with showrooms closed until April.”
Indeed, the winners of the crisis appear to be those who didn’t cancel orders in the face of the pandemic or those who have secured good long-term access to supply. Manufacturers such as Hyundai, Toyota and BMW appear to be relatively unscathed. A BMW spokesman has confirmed that ‘the supply of electronic components has been ordered to satisfy 2021 production’.
One area that hasn’t suffered is demand for new vehicles, according to Leasing.com figures.
“New car demand via Leasing.com has actually grown each month in 2021 and our audience has been particularly interested in physical stock they can access within a matter of weeks,” Harrison points out.
“Many consumers will have held onto their existing lease vehicle for longer during the pandemic and want to get into their next vehicle as quickly as possible. Semiconductor supply is set to improve in Q3 and in the meantime, our advertising partners are doing a great job of maintaining demand by offering consumers enticing deals on factory ordered vehicles.”
“There is large pent-up demand which means we will go from famine to feast as soon as there is a free supply of microchips,” Cousins agrees.
Diversifying supply
The semiconductor shortage is not just being felt in the auto industry, but across the electronics industry, everywhere from mobile phones to gaming consoles. Preventing this from becoming an ongoing problem is going to require a widespread response.
“For me, this is not just a manufacturer issue, it is a country infrastructure issue, in fact, similar to the requirement to build battery giga factories; other governments are already taking action,” Cousins says.
“The EU has set a plan to double current production, thereby controlling 20% of global output. Joe Biden has approved $50bn for additional semiconductor production and establishing centres of excellence in places like Arizona where Intel and TMSC are investing a combined $32bn in new facilities.”
Cousins also points out that we have yet to see any action from the UK government on this, but the UK is starting from a position of no capability, and so productive action is difficult.
“Individual companies will of course be trying to maximise their supply and undoubtedly costs will go up as there is increasing interdependence between the electronics and automotive supply chain,” Cousin tells us. “The good news is that semiconductor manufacturers are increasing production, including people like Robert Bosch.”
Even once solutions are in place, however, this crisis will have revealed a serious vulnerability in the industry.
“The semiconductor shortage has, therefore, highlighted the overdependency of the automotive sector – as well as most others – on small yet disparate supply chains,” Harrison says. “There is a need to diversify supply networks at a national and international level.”